OPT contributed new breakthroughs in visual applications of lithium battery industry
Release time:25.05.2022
Source :
In the environment of intelligent production process, the introduction of machine vision has greatly increased the defect detection rate, which has improved the production capacity and efficiency of the lithium industry.
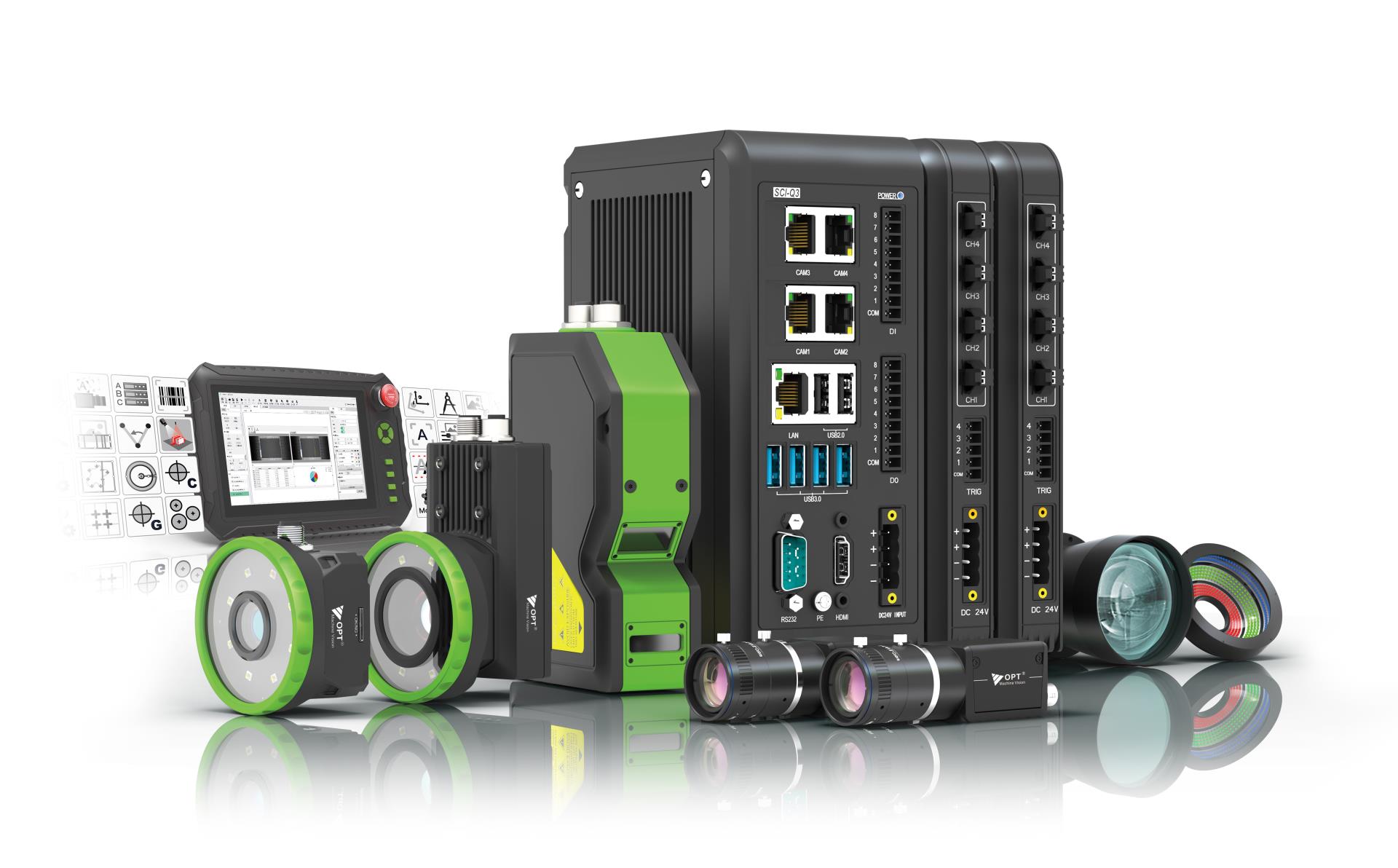
OPT Machine Vision Components
In view of the increasing market requirements, OPT Machine Vision focuses on continuous technological innovations and product optimizations in software and hardware. This ensures that the rapid development of the lithium industry can be kept pace with.Software
In the field of software, innovations of algorithms have been carried out. The vision software developed by OPT is designed for high-speed inspection of lithium batteries. It has extensive and complete function modules that ensure the high processing speeds of the algorithms.
OPT's Deep Learning software has many advantages for fault detection, such as
•flexible data annotation,
•automatic model generation,
•model learning,
•high confidence in model result evaluation,
•and other features.
It effectively solves the problems of conventional algorithms in complex scenarios, such as low robustness, low detection accuracy, and low adaptability.
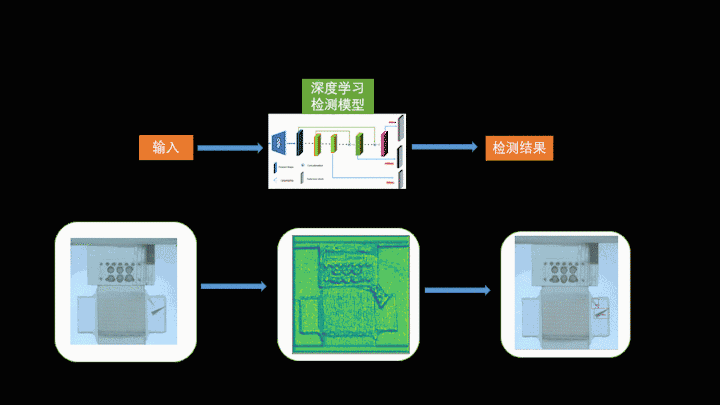
Deep Learning Fault Detection Scheme for Lithium Batteries
To meet the demand of the market, OPT has launched its own self-developed intelligent machine vision software. This is not only more accurate and faster, but also clearer and easier to use when developing applications.
The software is operated using graphical programming (GUI) instead of cumbersome source code programming. This allows the user to quickly implement machine vision projects through parameter configuration, which significantly reduces project development time.
Overall, the design and process of an optical inspection is greatly simplified. This is evident in the reusability of an application and also in the triggering mechanisms of subsequent processes and events. The quality control and inspection requirements of the lithium industry are thus optimally fulfilled.
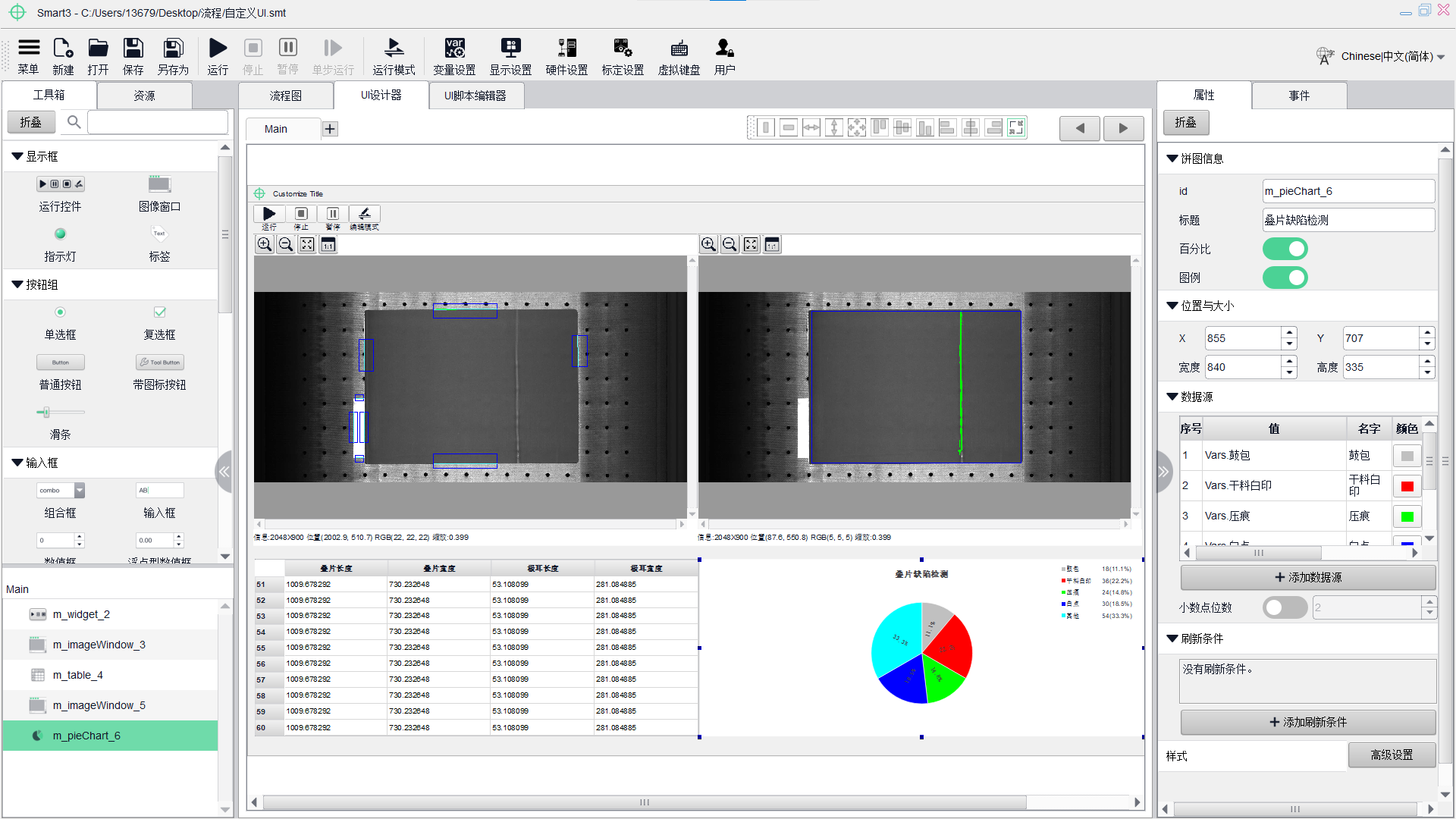
Graphical user interface (GUI) of the Smart3 Intelligent Vision Software
Hardware
In the field of hardware, product optimizations are continuously carried out through constant iterations. This permanently satisfies all requirements of applications in the lithium industry: from cameras, lenses and light sources to 3D laser contour scanners and industrial code readers.
Line Scan Cameras
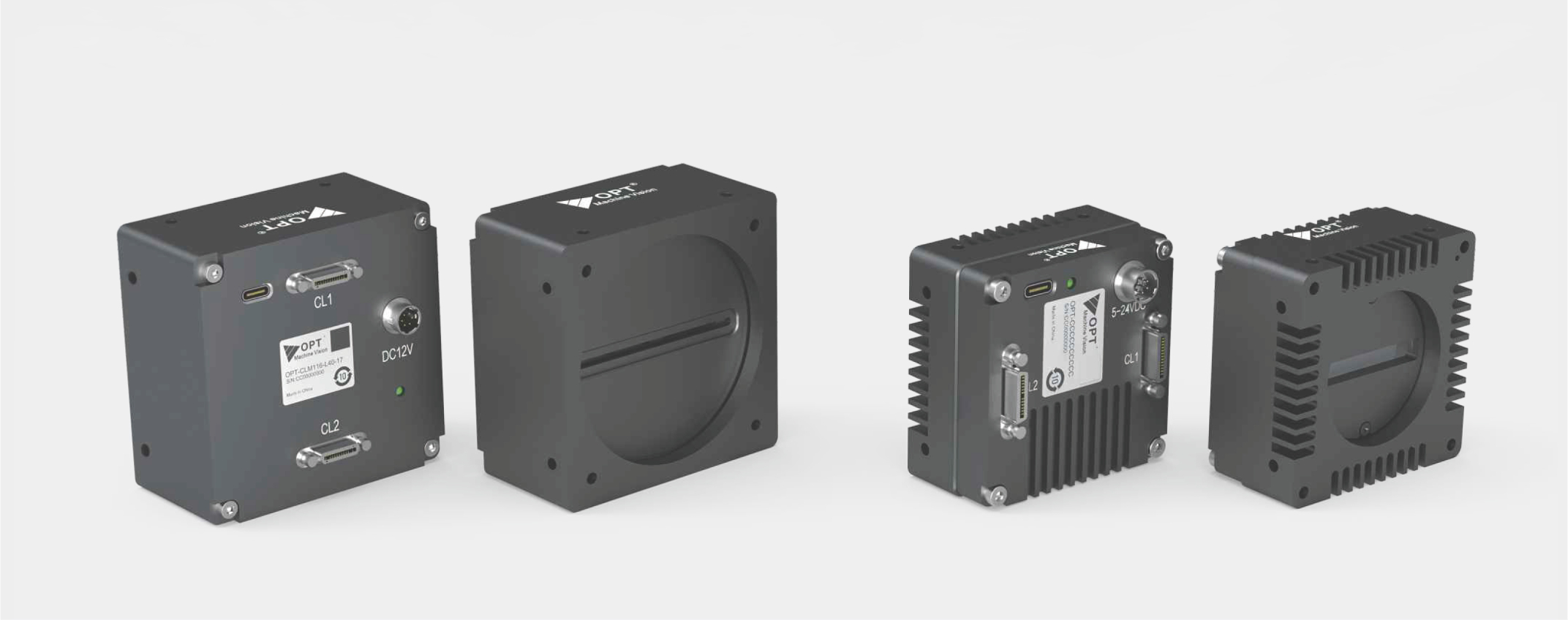
Line Scan Cameras
■ Product Features
-Resolution range from 2k to 16k.
-High speed, high sensitivity and low noise.
-The cameras contain a high speed image line sensor, large format programmable logic gate array. Image data are output externally via a high-speed industrial camera link bus.
Line Scan Lenses
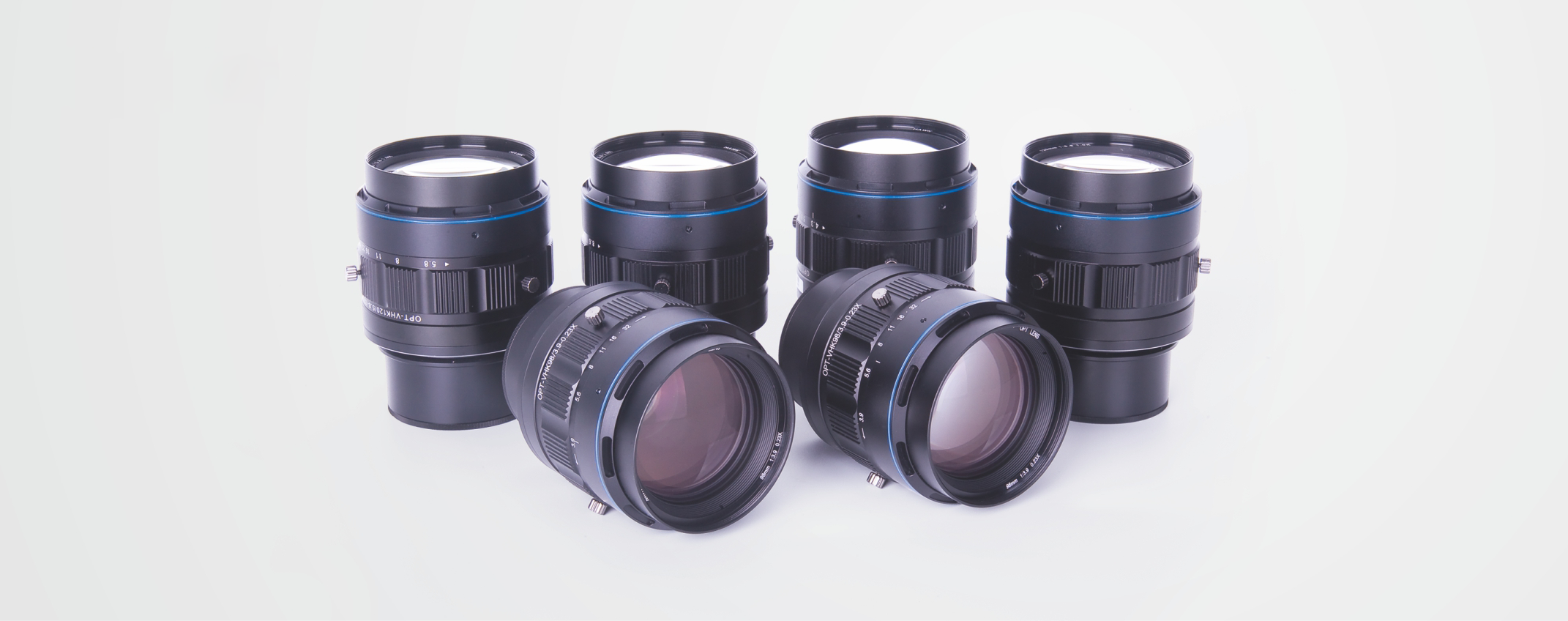
Line Scan Lenses
■ Product features
-High accuracy and low distortion.
-Lenses for 4k, 8k and 16k line scan camera applications.
-Especially suitable for high resolution LiPo inspections.
Industrial line scan camera lights
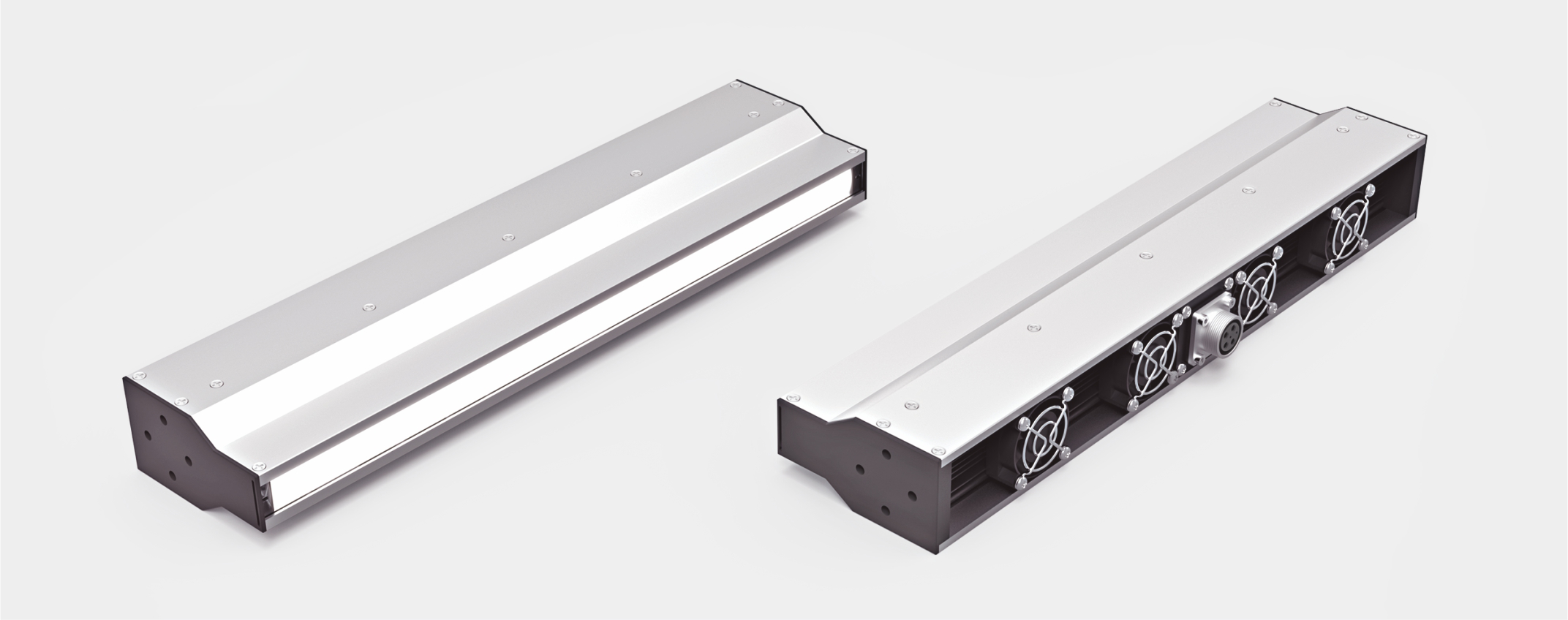
Industrial line scan camera lights
■ Product features
-High brightness and high uniformity. Line light source with a brightness of up to 5 million Lux. Suitable for inspection of e.g. lithium front panels.
-Compatible with reflective and non-reflective materials.
-Small light divergence angle, applicable with various working distances.
3D Laser Profile Scanners
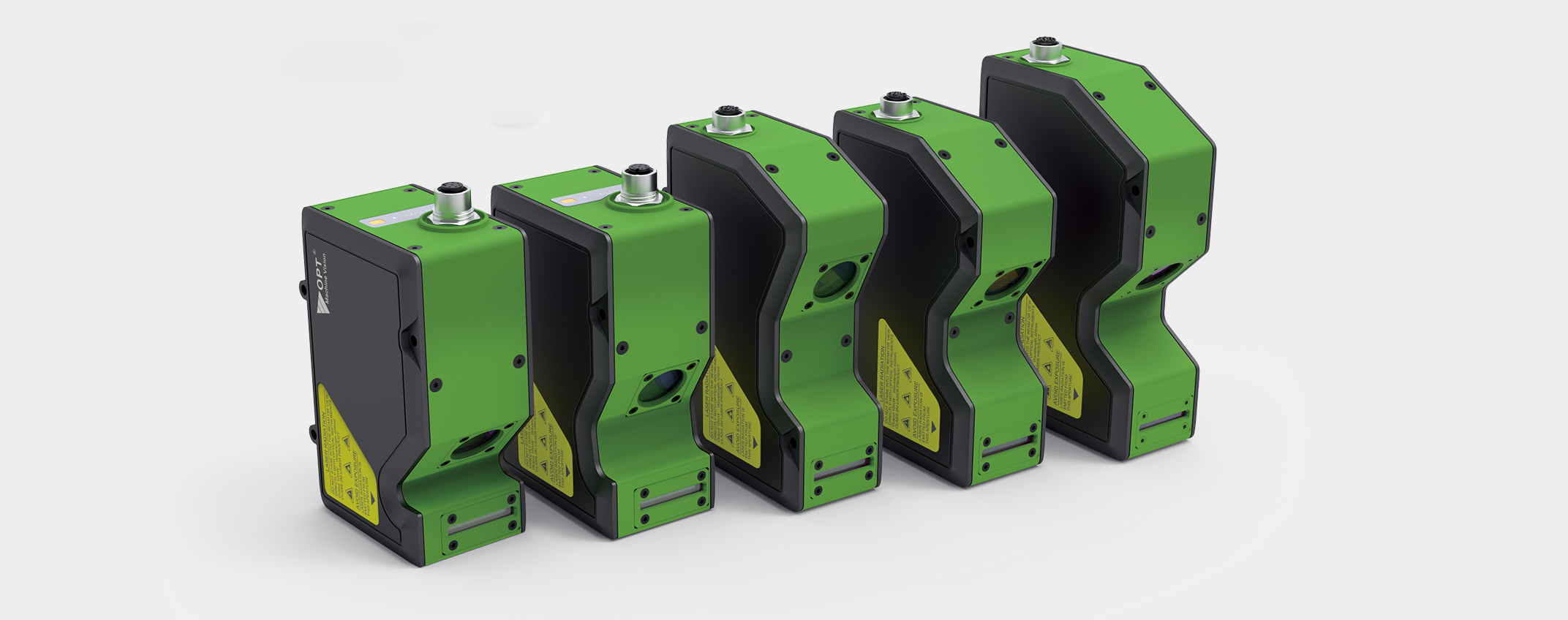
3D laser triangulation profile scanner
■ Product features
-Up to 3,200 pixel points in horizontal direction (X-axis).
-Scanning speeds of up to 67,000 contours/second.
-Flexible configuration and integration of 3D and 2D algorithms.
-Special 3D algorithm for detecting defects in the weld after laser welding, automatic discrimination of defective welds with short and stable commissioning cycles.
Industrial Code Readers
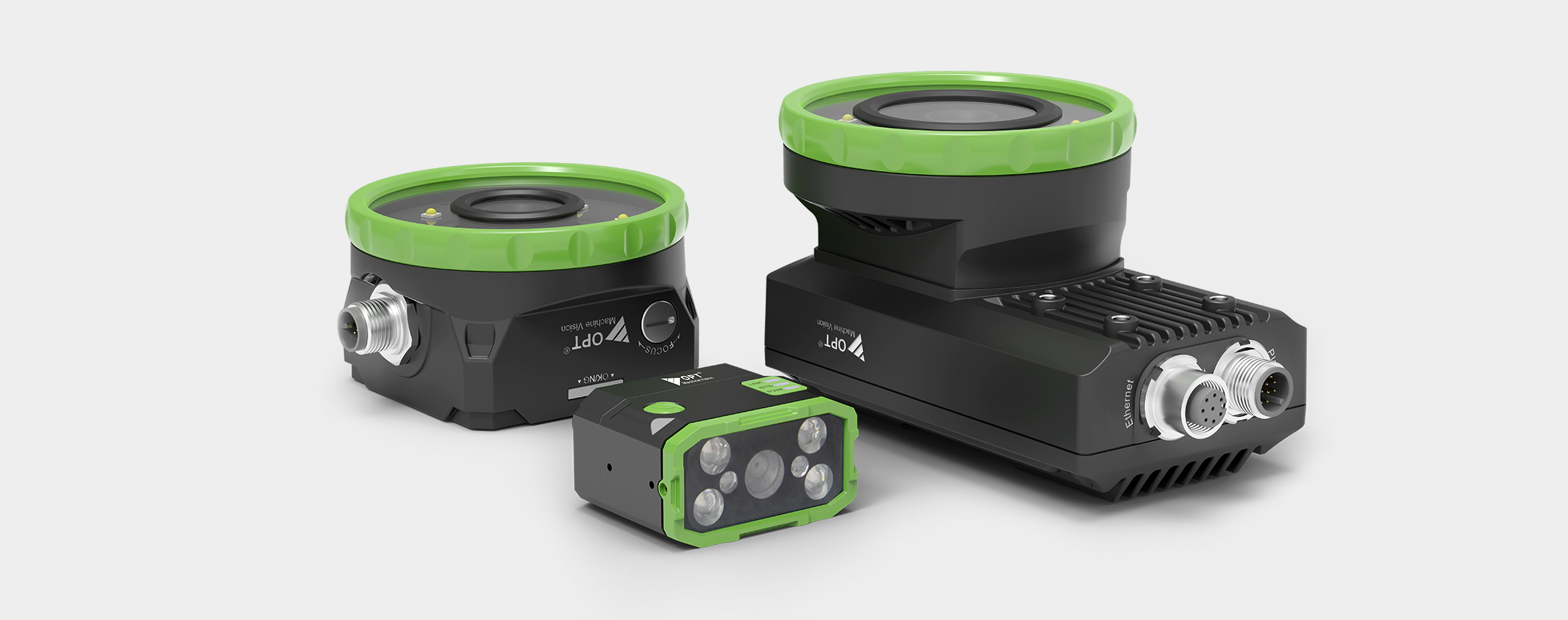
Industrial Code Readers
■ Product Features
-Integrated controllable light source, can realize reading a code by split controlling the light source.
-Built-in deep learning algorithm to read codes, efficiently read various barcodes and 2D codes.
-Extensive communication interfaces, supports TCP/IP, ProfiNet, EtherNet IP, FTP and other common communication protocols.
For all machine vision applications in the lithium battery industry, OPT has many years of technology development and practice and is now able to fully cover all machine vision applications in all lithium processes.
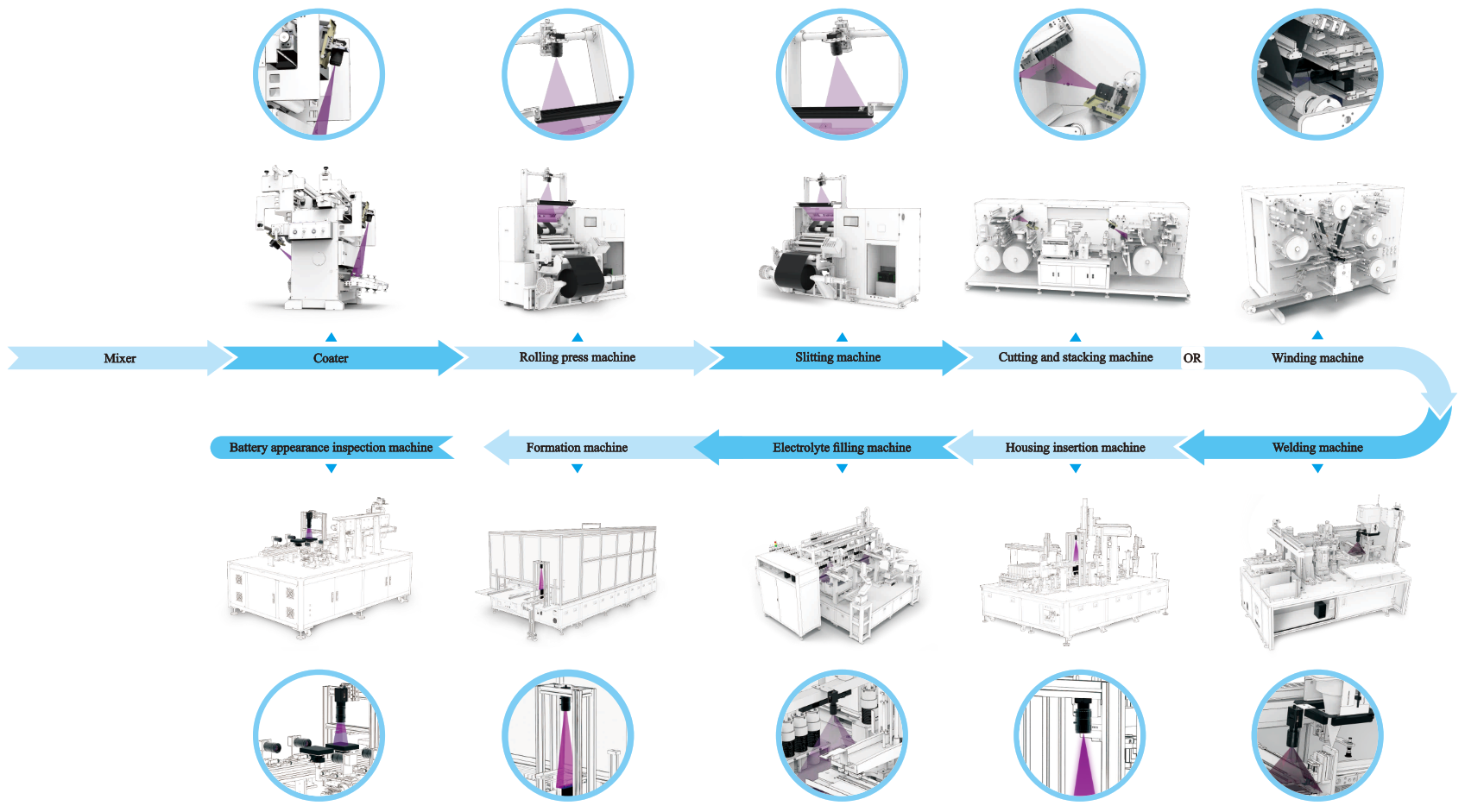
Machine vision application areas in the lithium battery industry
Typical Applications
Laser Cutting Machine
The laser cutting process cuts out the pole pieces with a laser, and the machine vision detects typical defects (metal leaks, breaks, residual material, marking holes, splice bands, bubbles, decarburisation, white spots, etc.) and measures dimensions (pole length, pole width, pole piece height, slot width, etc.) online and in real time during the production process. The software makes closed-loop corrections based on slot sizes, lug heights, etc. In addition, it marks defective pole pieces.

GUI of a laser cutting application
■ Inspection requirements
-Detection of surface defects on the front and back of the pole piece.
-The width of the pole piece before slitting.
-The width of the AT9 cathode.
-Size and appearance of the pole lugs.
-Width of pole piece after slitting, EA.
■ Inspection solutions
-High-speed line scan camera + area camera,
-output of correction data,
-real-time processing of all types of defects and dimensions to be marked,
-uploading of data.
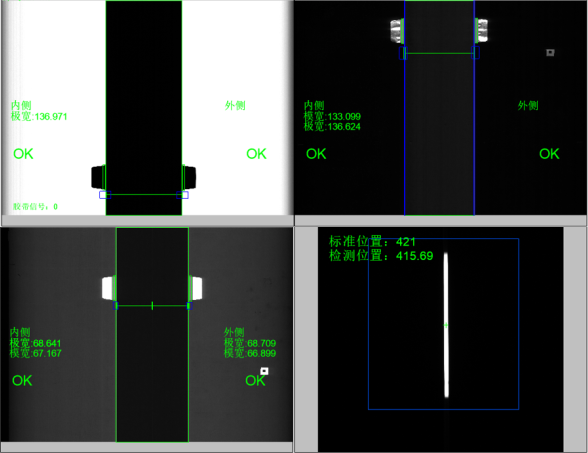
Inspection results
Detection of welding defects on lithium batteries
When detecting lithium defects, it is usually necessary to detect welding defects (burst spots, missing welds, welding holes, cocked nail welding, nail-less welding) on the sealing pins of the battery case cover to ensure the safety of lithium batteries.
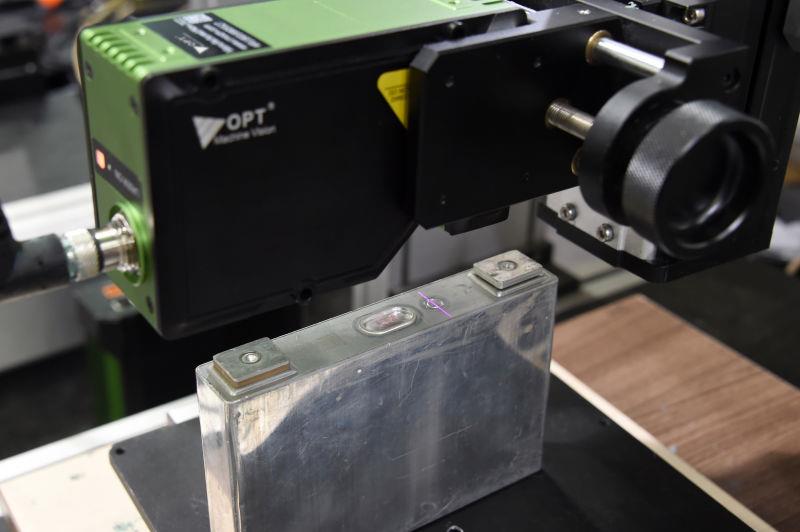
Laser triangulation sensor
Due to the unpredictable nature of post solder patterns, it is difficult to display all defect features when conventional cameras are used for inspection. In practice, 3D inspection technology with AI and defect algorithms can effectively distinguish between defect types.
Inspection solutions
The weld itself is generally uneven and varies slightly in height. Defects, however, often have abrupt changes in height. To measure and detect the height defects in the welds, 3D laser profile scanners and special 3D algorithms are used after laser welding. Based on this information, the areas with unacceptable height variations are marked.
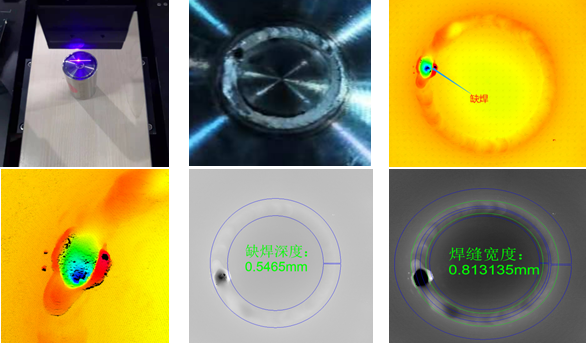
Inspection results